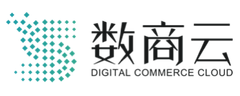
眼下工业互联网、智能工厂等概念非常热,无论从国家政策引导、企业自身诉求还是资本关注的热点,对这些都有非常美好的规划和设想,在技术方面也不断取得进步提升,再加上人口结构的变化、愿意从事一线产业工作的年轻人不论从绝对数量还是相对比例上都在不断下降,大家看到机器人、人工智能、物联网、工业互联网等技术在不断涌现,似乎很多以前靠人来完成的工作都可以由机器和算法来实现,于是,“无人工厂”成了一个非常诱人的想法和期待。
大家都对特斯拉汽车工厂科幻片一般的制造场景津津乐道,期待这样的场景能够在更多的工业制造中实现,觉得这代表了未来、代表了强大的生产力。
化工厂一直以来都给人以安全环保问题突出、过程不够高大上(比如会误解为化工的自动化程度低)的印象,前些年因为一些安全环保问题,更是在社会上造成了谈化色变的尴尬局面,甚至有些不负责任的媒体污名化化工行业,这令人十分痛心,也促使我们这些化工人在内心里挣扎一个问题:我们化工行业真这么不招人待见吗?
事实上,化工是国民经济的支柱产业,中国化工行业去年的总产值是14.2万亿,占了我们国家GDP的14%,中国化工在全球的占比已经高达40%。我们环顾周边,你身边用的哪一样材料不是通过化工行业生产出来的?供养中国14亿人口的粮食,并不完全是袁隆平院士的功劳,这里面还有更大的贡献来自化肥。
这里插一句题外话,最近听到一个国外智库报告,预计很有可能会出现全球性的粮食问题,这其中最主要的一个因素是俄乌战争,这两个国家都是粮食出口大国,更重要的是,俄罗斯是全球化肥出口大国,因为俄罗斯有丰富的天然气,因为俄乌战争,西方对俄罗斯实行全方位的制裁,影响俄罗斯化肥出口,进而影响全球粮食生产。
很多人因此就想,既然化工生产这么多的安全环保问题,那是不是可以让化工厂实现全面自动化,以至于实现“无人工厂”?
这里我要说这是难以实现的美好幻想。
我认为化工厂可以努力少人化,但是无人化是不可能的,至少短期内是不可能的。我认为我们不要试图追求无人化,而是应该怎么给人赋能,让化工人更安全,工作更高效。
化工厂不能实现无人化的根本原因在于化工生产管理是需要将机械化、自动化等的“机器智能”与“人的智能”很好的结合起来。
化工,是以化学反应过程为核心的工业生产。
化学反应与物理过程的一个重要差异在于化学反应难以有精准的数理方程描述,化学反应受多因素的影响,浓度、温度、压力、催化剂性能等,还有复杂反应(并行反应、串联反应、主副反应相互影响),还有反应平衡(热力学因素)、反应速率(动力学因素)等相互作用,所以对于工业上的一个反应过程,往往只有近似模型描述,这类近似模型有其适用边界条件。
化学工业还经常是多流程耦合,上下游之间相互影响。
这样的具有内在模糊性、流程耦合高度复杂的体系,又伴随着有毒有害物质、易燃易爆风险的系统,在一些主流化工生产企业,都已经有DCS、SIS、PLC等先进的自动化系统管控,我们化工的自动化水平在工业领域是处于领先的,而不是像人们印象中的那样认为化工生产方式比较粗放落后。
但是因为化工生产的复杂性,仅仅依靠自动化这样的“机器智能”还是不够的,因为很多情况是无法建立自动化执行方案的,化工生产依然离不开“人的智能”。
对工厂来说,并不是只关心处于正常生产的状态,系统开停车阶段就是非常关键的环节,这时候流程和设备很多是偏离正常设计条件下运行的,需要生产组织者面临随时可能出现的突发情况,一个团队是否有处理复杂局面的“肌肉记忆”是衡量团队是否优秀的重要依据。
工厂有大量的各类设备,这些设备都需要日常的保养维护、故障处理,这些又是工厂是否能处于良好状态的重要基础,就像人,需要有好的生活方式作息规律,定期体检,发现问题要及时处理。
对这些问题的处理都离不开高素质的人。
简单追求“无人工厂”,就会失去对这些异常状态的处理能力,也不能指望人在缺少实践感知基础上能有应对复杂状态的快捷响应。
人的智能主要体现在:模糊判断、弹性决策、灵活调整等人的思维的特征,这一方面能够弥补“机器智能”的僵化,在出现各种复杂局面时人可以根据自身的知识储备、生产经验和当时的具体情况做出更加弹性灵活高效的决策。
人的智能在工厂中并不是在特定的某些岗位上起作用,更多的是我们工厂的生产管理体系已经将人的智能融入其中,我们工厂都有机电化仪的专业分工,也有从基层一线到车间中层、分厂、总厂的不同层级,是一个高度组织化的体系,这些体系中每一个岗位都是将人的智能内化到其日常工作中。
但是人在提供“弹性决策”的智能时,也会带来问题,这是人的特点所决定,比如责任心、知识经验等方面的差异都会对其决策的正确性和有效性带来不确定影响,知识经验只存在于人的头脑中,一旦人员发生变动,这样的经验和知识就被带走了,而没有能有效地沉淀在工厂。不同人的判断依据不同,导致决策的差异,更多的是并行决策,而不能形成知识的迭代。
所以我们认为,化工数字化建设,除了关注“自动化”这个点,还应该关注生产管理体系的数字化建设。
帮助不同层级的人员提升能力、降低事务性工作消耗,把时间精力聚焦在专业问题上,消除人为的随意性和不确定性,为人的决策提供快速全面的信息支持,将人的知识经验沉淀在系统中,既能被复用,又能不断迭代提升。
人的能力素质如果低于要求,就会成为负担,如果高于要求,就变成了资产。化工数字化建设,就要通过系统来提升人的能力,让人成为资产,并且这种提高是系统化可持续的。
首先,这个问题没有标准答案,每个企业、每个管理者都有自己的情况和关注点。
我这里想要提醒的是我们要时刻想清楚自己搞数字化建设的初衷是什么?
大家常挂在嘴边的化工生产的“安稳长满优”,这个顺序大概能反应出事情的轻重缓急,这5个字的顺序也基本上列出了从短到长的五块板。
一般来说,流程型的化工生产,其原料消耗、工艺过程、生产能力基本上是确定的,日常所要关注的是如何让工厂能够在安全稳定的前提下达到设计能力,在此基础上尽可能降低消耗,提高设备使用效率。一次非计划停车带来的损失少则数十万,多则上千万。
就我们接触的数百家化工企业而言,大家日常关注的大部分还是集中在如何消除企业的短板问题:一线工作能够真正落实到位、能够及时发现隐患并高效准确处理、工艺和设备处于良好运行状态。
对于流程性能优化等问题,企业管理者比较关注,但是仔细研究会发现,真正的“优化问题”,可能还是要消除短板问题:PID设定是否合理、设计的自动化控制能否有效投用、运行参数是否与设计条件接近或一致等。
对于真正意义上的优化,我们可能发现要实现优化的目标,还是需要坚实的基础,同样需要流程和设备处于良好状态,相关的优化措施能够有效执行,以我本人比较熟悉的大型煤气化生产工艺为例,我们想要达到良好的气化效率(有效气产率、原料煤和氧气消耗等),必须要关注煤质的稳定(分析数据要准确)、计量仪表的准确、设备性能的可靠。
所以,我们认为,当下数字化更应该关注的是企业的短板在哪里,把短板问题解决好了,原来的长板可以更长,或者说才有机会更长。
就我们服务过的200多家化工企业来看,我们发现一个非常有趣的现象,往往越是头部的企业,他们数字化建设的关注点越具体,把这些具体的点解决好了,就能串联起一张兜住底线的网,扎牢篱笆墙。
这个非常值得我们探索数字化建设路径的企业思考。
我们认为,化工数字化建设是一个企业生产管理模式的演化过程,并不是交付项目。
要做好这个过程,调动起一线的积极性和主动性是关键,一线既能反馈真实的需求场景,也是数字化建设推进的桥头堡。
企业一线人员日常需要处理的事情非常多,如果数字化建设对他们而言是在他们已有工作上增加出来的负担,那他们就会在内心产生抵触,不愿意接受新事物,这是人性使然,无法通过宣传教育来改变。
我们很多企业负责数字化建设的管理者大概都有这样的苦恼和担心:老板认为我们企业需要进行智能化数字化建设,这是企业未来发展的必然趋势,也愿意为此提供预算资金的保障。我们执行者接下来就会面临如何推进此项工作,如何给老板定期反馈进展。
如果失去了一线人员的参与,很容易陷入的局面就是轰轰烈烈开场、劳心费力规划、苦口婆心推进、黯然神伤结局。
这些年我们看到了很多企业的数字化建设规划都遇到了这样的问题。
我们分析其背后的原因还是落在了化工数字化是过程这个关键点上,本身数字化建设目前就没有现成案例可以参考照搬,而且工业软件的设计存在一个“不可能三角”:
功能完整:能够覆盖生产管理的全部场景
逻辑严密:让数据信息能够准确组织流动
体验良好:一线员工能够接受,不增加一线的负担
这三个目标是难以同时满足,不得不有所取舍。
怎么选取,并无一定之法,要看主要诉求是什么。大型管理软件,更看重功能完整和逻辑严密,比如SAP,或者欧美的大型安全管理软件(如gensuite),这些软件功能强大,底层扎实,但是这些软件经常被抱怨的是很难用起来,这就是很难实现良好的用户体验。
因为用户体验不仅仅是交互设计的问题,还要考虑跟用户工作习惯的匹配问题,这个问题如果不解决好,人就会觉得上这些系统是给他们增加了负担,而不是帮他们解决问题,越是基层一线,这个问题越突出,这个不是通过简单的宣贯教育就能解决的问题,这有人性在其中。
哈佛商学院变革大师约翰*柯特教授及麦肯锡的调研发现,70%的变革都是失败的,变革成功率只有30%,而其中只有10%的变革超出了预期。如何提升变革成功率?在GE内部有一个公式:
E=Q*A
E:是指变革成功,Q:决策质量,A:团队对决策的认同程度。
失败的变革项目90%都有一个很高的决策质量Q,但因为团队对目标缺乏认同度A而宣告失败。可见,人的因素是决定变革成败的关键因素。
企业的变革包括战略、商业模式、技术、流程与制度、企业文化、领导力、人才等变革,如果企业只想着改变战略、商业模式、技术等条件而忽略了人的因素,那么变革注定是失败的,因此企业变革的核心是管理变革,而变革成功的关键在于如何转变人心。
约翰*柯特教授在《引领变革》等著作中提出“变革八步法”:增强紧迫感、建立指导团队、设定愿景、感召众人、赋能行动、创造短期成效、再接再厉、巩固成果。
可以看出来,我们化工企业数字化建设在某种程度上就是一场变革,上述关于变革成败的分析完全适用,尤其是“变革八步法”,与我们数字化建设的目标、实现路径高度吻合,所以如何让一线员工感受到数字化给他们带来的帮助(赋能行动、创造短期效益),并且能够在此基础上激发出他们对数字化建设的真实需求(再接再厉),以达到真正落地数字化建设成果并不断形成与企业实际情况相贴合的系统(巩固成果)。
如何才能激发一线员工的热情?
我们的实践经验是要提供贴合一线日常使用场景的产品,并且能够让一线员工感受到数字化产品给他们工作带来了帮助:降低了工作复杂繁琐度,又给他们赋能。
在一线员工感受到了数字化产品的帮助后,就会激发出他们对数字化建设的认同,并源源不断产生新的需求,这些需求是真实的需求,相当一部分是有价值的需求。这些需求不断被满足,数字化建设就具备了自我生长的能力,能够生根发芽。
我们在服务企业过程中,深刻感受到伴随一线不断产生需求形成的产品,是具有强大生命力的。反而是一些早期规划时候做了很多美好设想的方案,后来能落地的不多。
所以回到我们所说的“不可能三角”,其中系统的友好度是一个非常值得重视的维度。
不断发展的IT技术也给化工生产管理带来了新的工具和方法, 这是可喜的一面。
但是这些快速发展的技术如何真正能够应用到场景中,还需要有可执行的方法,从企业的角度,我们要理解工厂的人员日常精力都是围绕他们自己的业务,难以对这些外部发展的技术有真切的理解和感受,而且如果只是零星地应用一些单点的技术,同样会面临工作量增加和不确定的预期结果。
所以我们看到很多有望提升生产管理能力和效率的技术总是在外围打转,美好的理想碰到了骨感的现实,总觉得传统行业的人是不是太土了,不能理解和接受新兴事物。
这个现象背后的原因说到底还是角度问题,外部供应商对于化工企业内部从事生产管理的真实工作状态和关注点缺乏了解认知。
文章来源: 中国石油和化工
编辑:云朵匠 | 数商云(微信公众号名称:“数商云”)
【数商云www.shushangyun.com】致力于提供企业级的电商平台服务,长期为大中型企业打造数据化、商业化、智能化的b2b交易系统解决方案,同时我们还提供B2B网站、B2B2C多用户商城系统、B2C电子商务系统、跨境进口电商平台、S2B2C平台、供应链管理平台,采购管理平台、渠道管理平台等一系列系统定制开发服务。通过大数据、云计算等新技术协助企业打造供应端—渠道端—营销端—数据端等全链数字化运营体系,提升企业运营效益与智慧数字化商业转型。